在齿轮淬火热处理生产中,六工位齿轮淬火机床通过工位分工优化,实现了加热与上下料的高效衔接。该设备虽命名为 “六工位”,但核心功能集中于单一加热工位,其余五个工位仅承担上料、下料及待处理环节,不参与预热、退火、回火等工艺,通过流程设计提升整体作业效率。
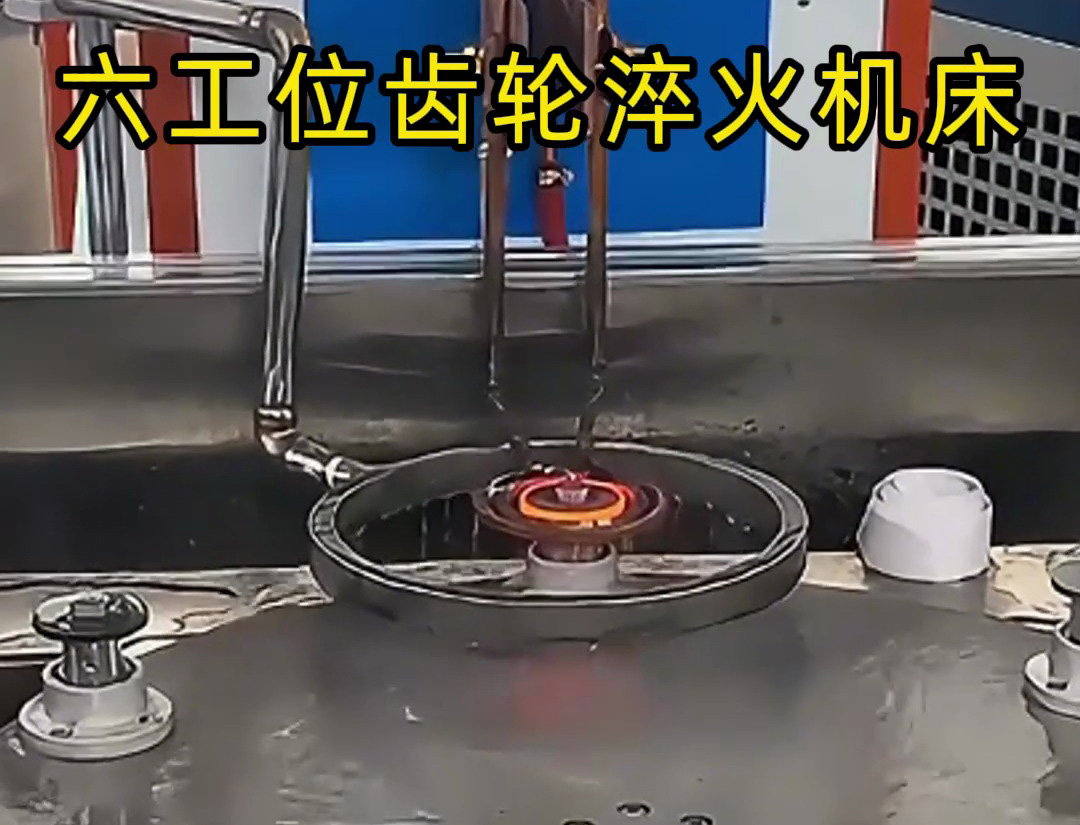
设备采用环形布局设计,六个工位沿转盘均匀分布,转盘由伺服电机驱动,可精准定位至各工位:
- 工位 1-2(上料区):操作人员将待淬火齿轮放置于工装夹具,完成定位与固定(工装采用三爪定心结构,确保齿轮径向跳动≤0.05mm);
- 工位 3(加热区):配备高频感应线圈,针对齿轮齿面或齿根进行局部加热(以模数 5 的齿轮为例,加热温度 860-880℃,时间 15-20 秒);
- 工位 4-6(下料区):加热完成的齿轮依次经过喷水淬火(冷却至 200℃以下)、工装松开、成品取放,实现与后续工序的衔接。
单一加热工位配合五个辅助工位的设计,解决了传统单工位设备 “加热时无法上下料” 的效率瓶颈。以直径 100mm 的齿轮为例:
- 传统单工位设备:单次加热 + 上下料总耗时约 40 秒,每小时产能 90 件;
- 六工位设备:加热工位持续工作(15 秒 / 件),上下料与加热同步进行,每小时产能提升至 144 件,效率提高 60%。
设备通过 PLC 控制系统实现全自动运行,加热参数(功率、时间)可预设存储,换型时只需调用对应程序,调整工装夹具(换型时间约 10 分钟),适配不同模数(2-8mm)齿轮的淬火需求。
加热工位的高频感应系统是质量控制的关键:
- 线圈设计:采用仿形齿部感应器,确保齿面加热均匀(硬度差≤3HRC);
- 冷却系统:环形喷水装置与齿轮同步旋转,保证淬火液(5% 聚乙烯醇溶液)均匀覆盖,硬化层深度控制在 0.8-1.2mm;
- 温度监控:红外测温仪实时监测齿面温度,偏差超过 ±10℃时自动停机报警。
生产数据显示,该设备处理的齿轮淬火合格率稳定在 98% 以上,变形量≤0.1mm,满足装配精度要求。
此类设备适用于中小规格齿轮的批量生产,尤其适合汽车变速箱、电机减速器等领域的标准化齿轮加工。日常维护需注意:
- 每日清理加热工位的氧化皮,防止影响感应效率;
- 每周检查转盘定位精度,确保工位切换误差≤0.02mm;
- 每月校准测温系统,保证温度检测准确性。
六工位齿轮淬火机床通过 “单一加热 + 多工位辅助” 的设计,在不增加工艺复杂度的前提下,大幅提升了齿轮淬火的生产效率,为批量热处理提供了兼顾效率与质量的解决方案。
|