针对铆钉、螺丝、螺母等小工件(尺寸≤20mm)的退火或淬火热处理,半自动 / 全自动高频设备通过 “振动盘上料 + 程序控温 + 自动化下料” 的全流程设计,实现批量生产的高效性与一致性,完美适配紧固件、小五金件的规模化热处理需求。
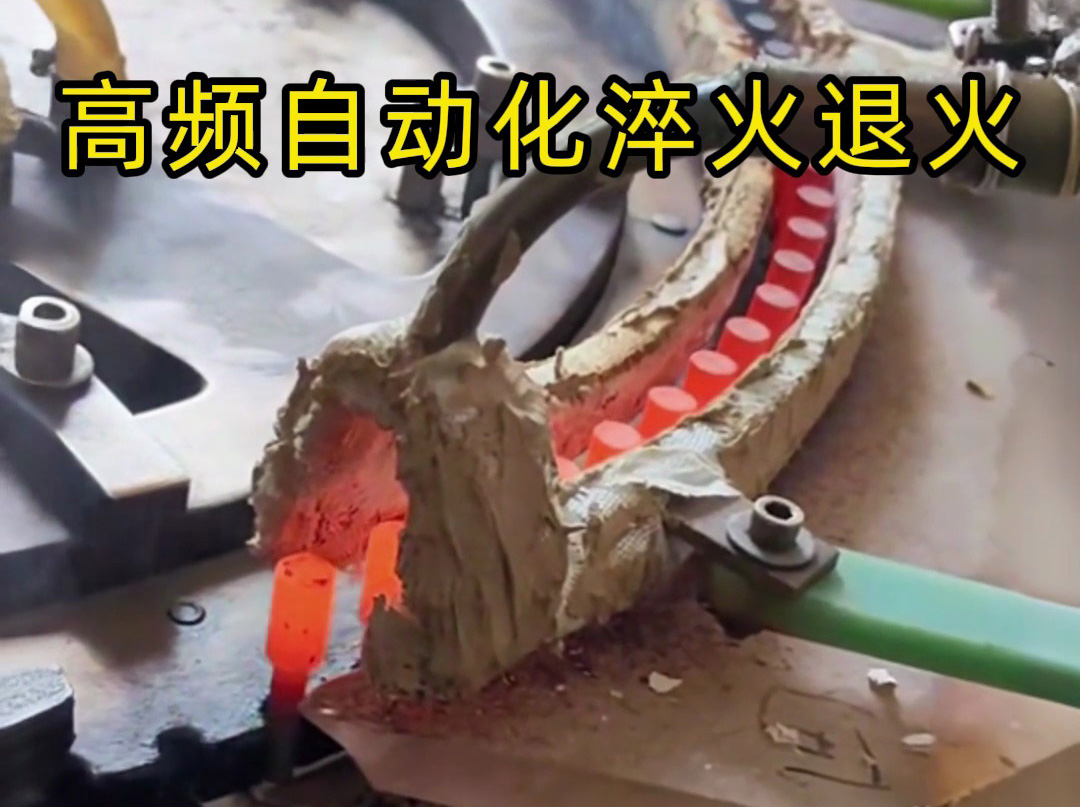
这套设备通过四大模块协同工作,将人工干预降至最低,单班(8 小时)产能可达 1-5 万件(根据工件尺寸):
- 定制振动盘:根据工件形状(如铆钉的圆柱形、螺丝的带槽头部)设计内部分料轨道,通过振动(振幅 5-10mm)使杂乱工件自动排序(如螺丝头部朝上、铆钉杆部向前),确保进入加热区时姿态一致(偏差≤0.5mm);
- 防拥堵设计:轨道末端设传感器,当工件堆积时自动降低振动频率,避免卡料(卡料率≤0.1%),上料速度可通过 PLC 调节(50-200 件 / 分钟),与后续加热节奏匹配。
- 感应线圈定制:针对小工件设计微型线圈(内径 3-15mm),如螺丝头部淬火用 “环形线圈”(聚焦头部),铆钉杆部退火用 “管状线圈”(覆盖杆身),确保加热区域精准(非处理区温度≤100℃);
- 程序控温逻辑:
- 淬火工艺:设定加热温度 850-900℃(中碳钢),时间 2-5 秒(根据工件厚度),冷却水压 0.3MPa,确保表面硬度达 HRC55-60;
- 退火工艺:设定加热温度 600-700℃,保温 1-3 秒(消除冷加工应力),随炉冷却,使工件硬度从 HRC35 降至 HRC20-25(便于后续塑性加工);
- 实时监测:红外测温仪对准加热区,温度偏差超 ±5℃时自动调节高频功率(5-15kW),避免过烧或加热不足。
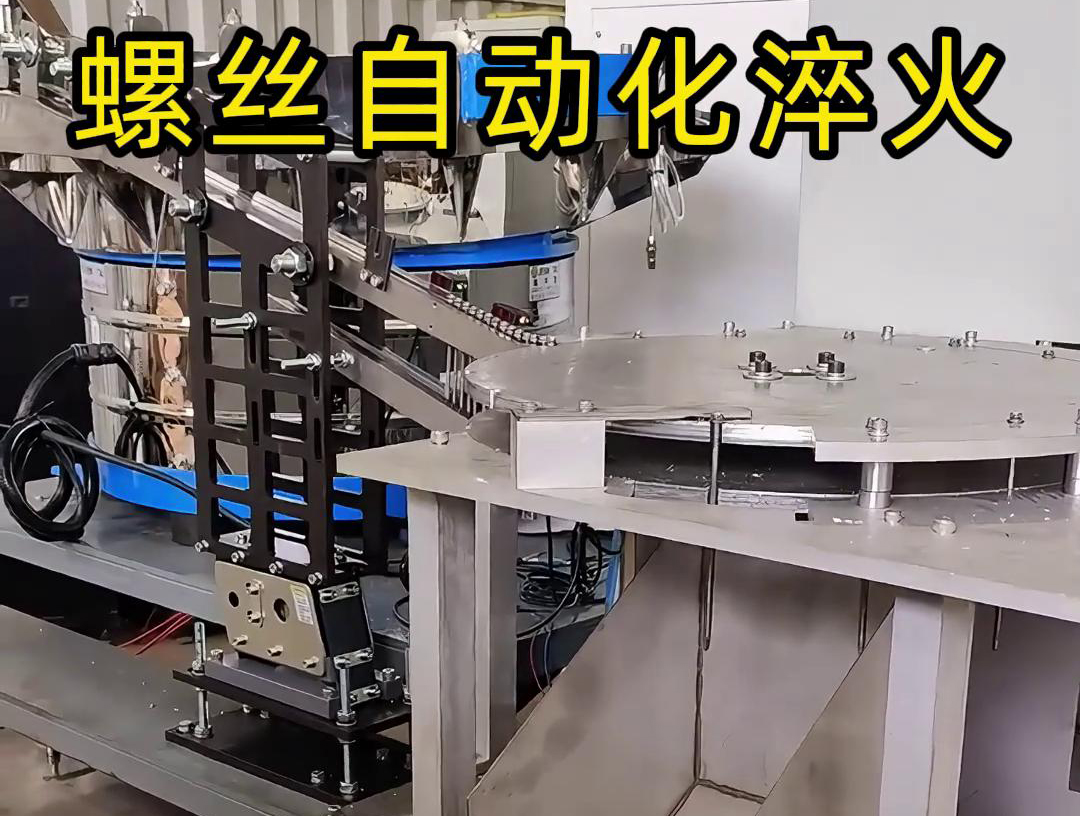
相比人工手持加热或传统箱式炉处理,这套设备的优势体现在:
热处理一致性提升至 99%
人工操作时,加热时间、距离全凭手感,导致同批次工件硬度偏差 ±5HRC;而设备通过程序固定参数(时间 ±0.1 秒,温度 ±3℃),螺丝头部淬火后硬度偏差可控制在 ±1HRC 内,满足紧固件的强度要求(如 8.8 级螺丝的硬度标准)。
能耗降低 60%,成本更优
微型线圈仅加热工件本身(如 φ5mm 螺丝,加热能量集中于头部 2mm 区域),热损失少;而箱式炉需加热整个炉膛(空耗大),能耗是高频设备的 2-3 倍。按日处理 1 万件计算,年电费可节省 3-5 万元。
解放人工,适配柔性生产
设备启动后仅需 1 人监控(处理异常卡料),无需人工上料、下料,对比 “2 人 / 班” 的传统线,年人工成本降低 10-15 万元;且更换工件时,仅需更换振动盘和线圈(30 分钟内完成),程序调用对应参数(如 “M5 螺丝淬火”“φ3 铆钉退火”),支持多品种切换(最小批量 500 件)。
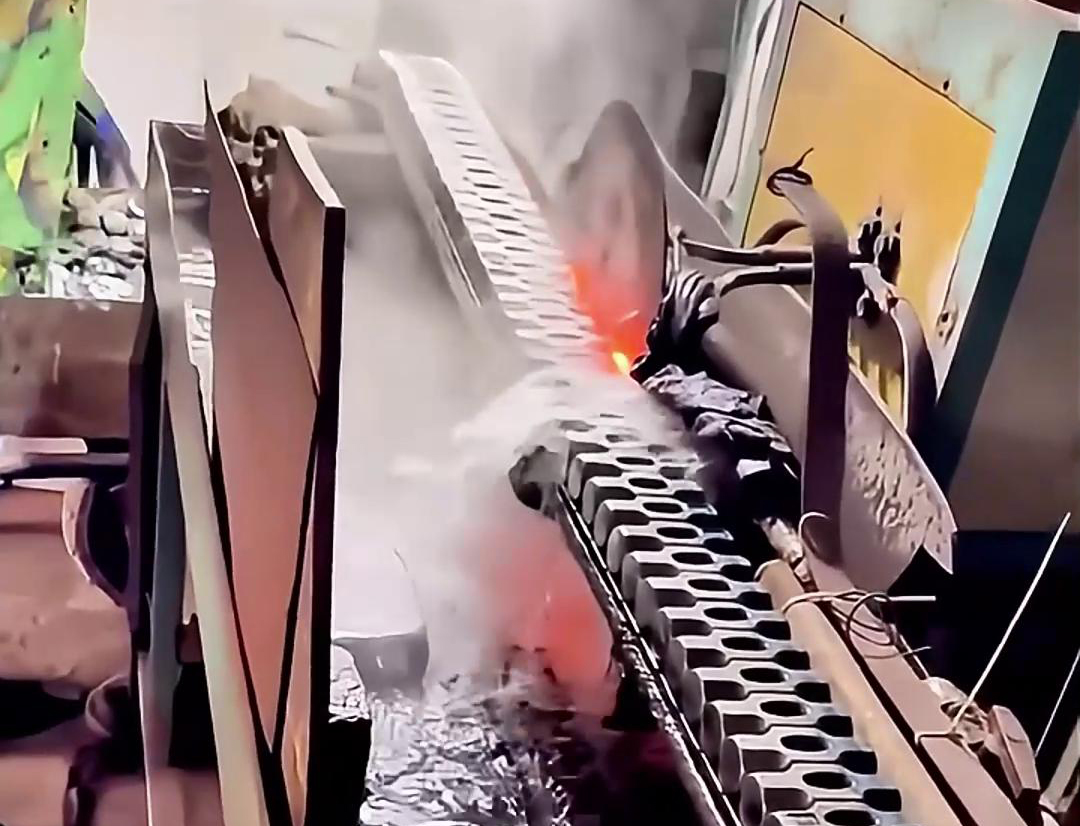
- 螺丝 / 螺栓淬火:建筑用膨胀螺丝、汽车底盘螺栓的头部与杆部过渡区淬火,设备可精准加热应力集中区(硬化层 0.3-0.8mm),抗剪切强度提升 30%,避免安装时断裂;
- 铆钉退火:航空铆钉冷镦成型后,杆部存在冷作硬化(易脆断),通过 650℃退火消除应力,延伸率从 10% 提升至 25%,铆接时不易开裂;
- 螺母内孔淬火:高强度螺母的内螺纹表面淬火,微型线圈伸入孔内加热,硬度达 HRC50-55,配合螺栓拧紧时耐磨寿命延长 2 倍(避免滑丝)。
这套全自动高频热处理设备,本质是通过 “小工件专属自动化设计” 破解了紧固件行业 “批量大、要求严、成本敏感” 的痛点。它以 “精准控温 + 高效节能 + 少人化” 的优势,将铆钉、螺丝等小工件的热处理从 “粗放加工” 升级为 “精密制造”,成为小五金规模化生产中 “质量与效率平衡” 的核心设备。
|