钢锯片(如高速钢锯片、合金工具钢锯片)的切割性能核心取决于齿刃硬度与本体韧性的平衡 —— 齿刃需承受高频摩擦(HRC60-65 可确保耐磨不卷刃),锯片本体需保持韧性(避免切割冲击时断裂)。超高频淬火(频率 500kHz-2MHz)凭借 “超浅硬化层 + 瞬时加热” 特性,成为钢锯片齿刃强化的理想工艺,完美实现 “刃口硬、本体韧” 的性能分化。
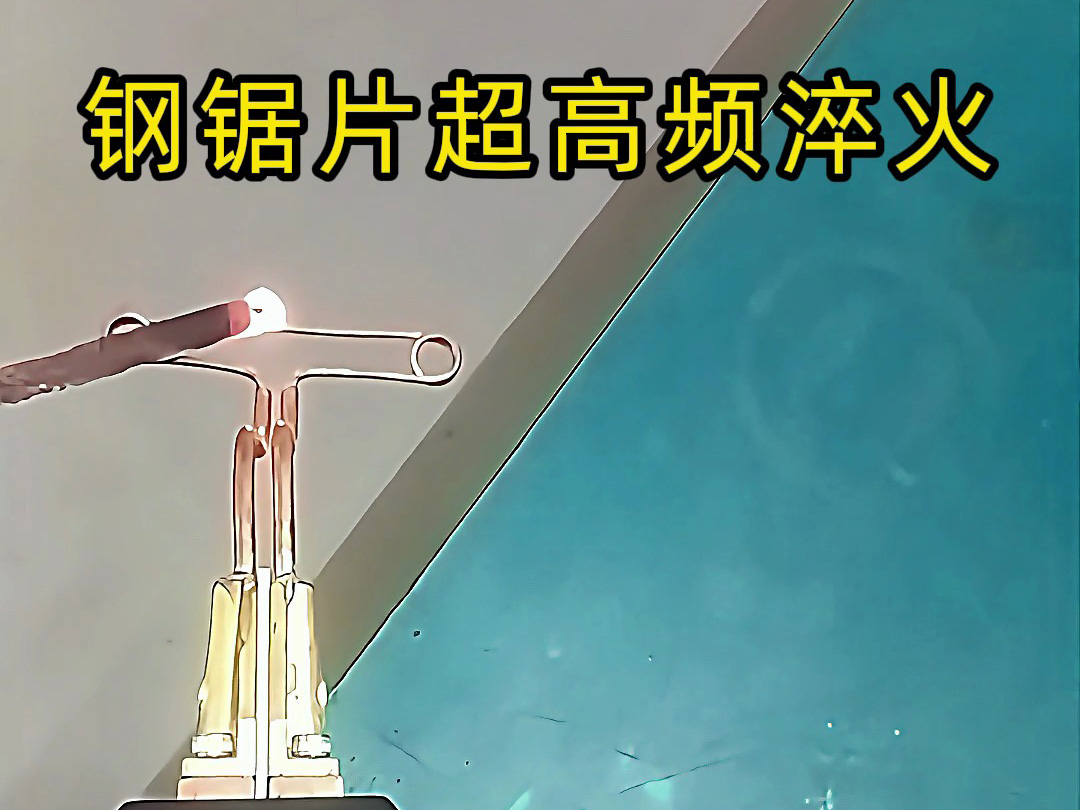
钢锯片传统淬火(如高频淬火、箱式炉淬火)常面临 “齿刃硬化层过深导致本体脆化”“加热不均导致齿刃硬度偏差大” 等问题,超高频淬火通过以下方式突破瓶颈:
- 趋肤效应极致聚焦:500kHz-2MHz 超高频电流的能量集中于齿刃表层 0.1-0.5mm(仅齿尖磨损区域),硬化层深度严格控制在 “耐磨需求” 范围内,锯片本体(距齿刃 2mm 以外)硬度保持 HRC30-35(韧性充足);
- 避免本体脆化:传统高频淬火(10-100kHz)硬化层达 0.8-1.5mm,易导致锯片弯曲时断裂(断裂率 10%-15%),超高频淬火使锯片抗弯曲性能提升 40%(可承受 15° 弯曲不变形)。
- 秒级升温控温:齿刃从常温升至奥氏体化温度(850-900℃)仅需 0.3-0.8 秒(远快于钢的氧化速度),氧化皮厚度≤5μm(传统加热氧化皮达 20-50μm),无需后续打磨即可保持齿刃锋利(齿尖圆角≤0.05mm);
- 微小热影响区:加热区域仅限齿刃尖端(宽度 0.5-1mm),锯片整体温度≤100℃,热变形量控制在 0.02mm/m 以内(确保锯片平整度,避免切割时 “跑偏”)。
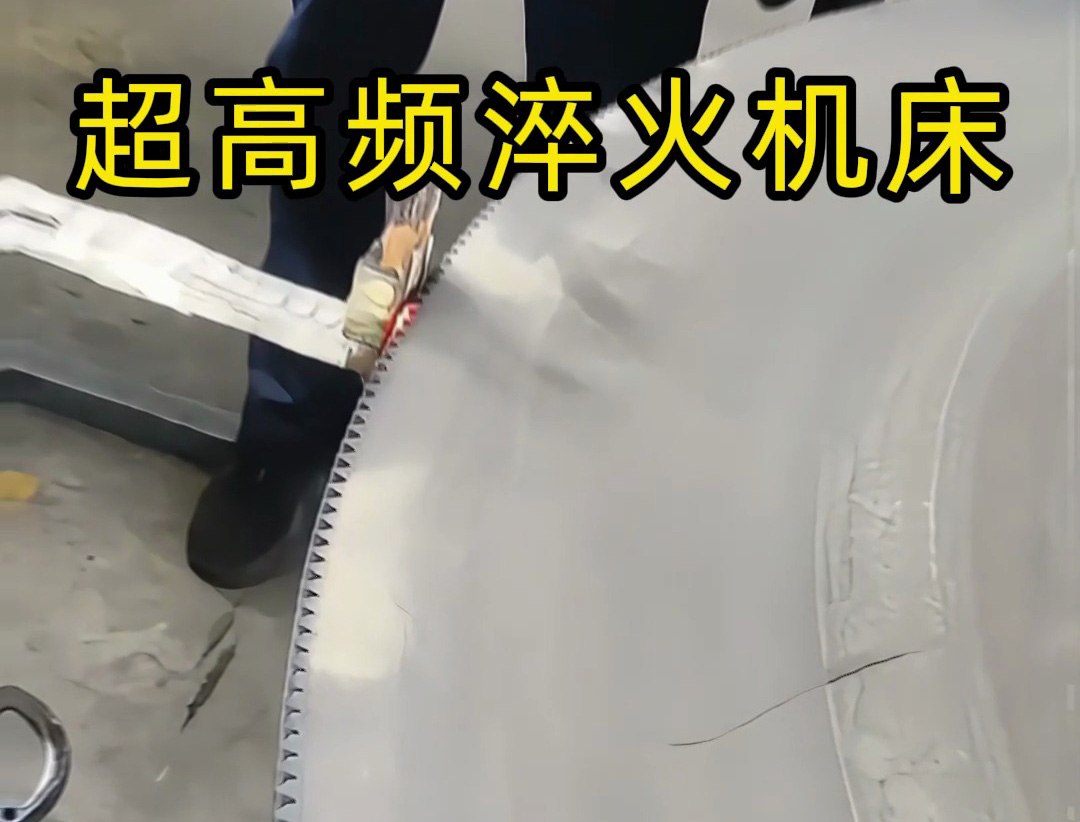
超高频淬火的钢锯片,在以下场景中展现出不可替代的优势:
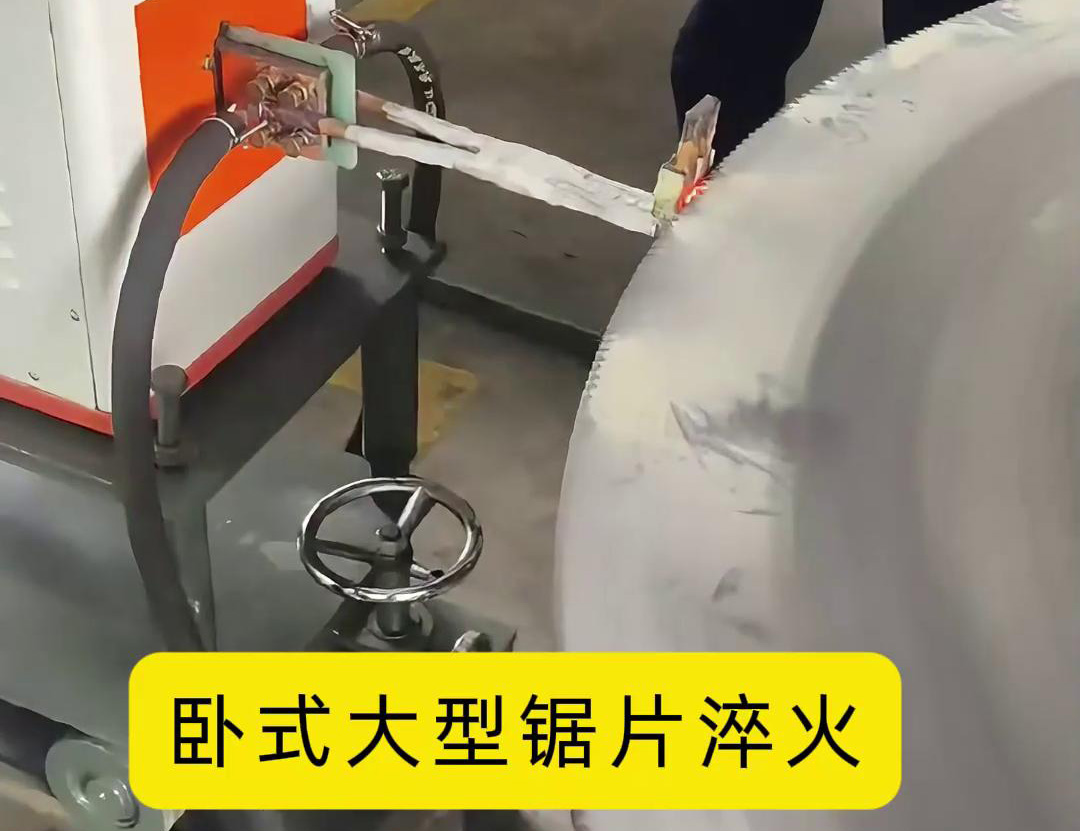
对比项 | 超高频淬火(500kHz-2MHz) | 传统高频淬火(10-100kHz) | 箱式炉整体淬火 |
---|
硬化层深度 | 0.1-0.5mm(仅齿刃磨损区) | 0.8-1.5mm(易波及锯片本体) | 全齿硬化,深度 1-2mm |
齿刃硬度 | HRC60-65,偏差 ±1HRC | HRC55-60,偏差 ±3-5HRC | HRC50-55,均匀性差 |
锯片变形量 | ≤0.02mm/m(平整度高) | ≤0.1mm/m(需校直) | ≥0.2mm/m(变形大,报废率高) |
使用寿命 | 切割次数提升 3-5 倍 | 切割次数提升 1-2 倍 | 基本无提升,易卷刃 |
超高频淬火对钢锯片的处理,本质是通过 “能量的极致聚焦” 实现 “齿刃精准强化”—— 既保证了切割核心区(齿刃)的高硬度与耐磨性,又最大限度保留了锯片本体的韧性与平整度。对于追求 “高精度、高效率、长寿命” 的切割场景,这种工艺是钢锯片性能升级的 “最优解”,直接推动切割工具从 “频繁更换” 向 “持久高效” 转型。
|